How to Install Air Compressor Lines: Step-by-Step Guide for Efficient Operation
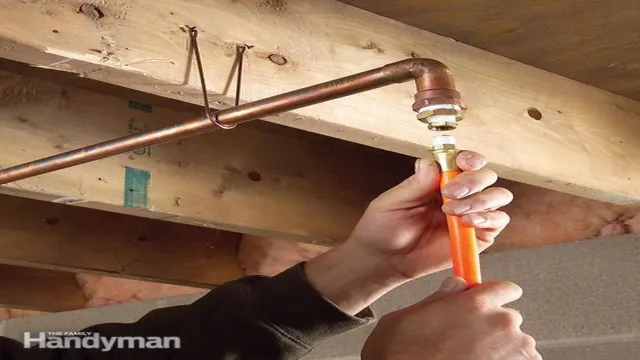
If you’re planning on setting up a workshop or garage, or just need compressed air for various DIY tasks, you’ll undoubtedly need air compressor lines. However, installing these lines can be quite a daunting task, especially if you have no prior experience. But fret not.
In this step-by-step guide, we’ll walk you through the process of installing air compressor lines effortlessly. By following this simple guide, you’ll learn everything you need to know to set up and maintain your air compressor lines correctly. Whether you’re a professional contractor or a DIY enthusiast looking to get handy with your tools, this guide is essential to ensure that your air compressor lines operate safely and efficiently.
So, let’s dive in!
Gather Your Materials
If you’re planning to install air compressor lines, the first definite step is to gather your materials. Make sure you have the right-sized pipes and fittings for your project. You’ll also need Teflon tape, wrenches, pipe cutters, a drill, and drilling bits.
The number of pipes and fittings you’ll need will depend on your project’s size and scope. It’s important to note that when selecting your materials, it’s best to go for high-quality, durable options as you’ll want to ensure long-lasting productivity and safety. Once you have all your materials in place, you can move on to the actual installation process.
Remember that taking your time to ensure everything is done correctly during installation will save you from future headaches and additional expenses.
Air compressor
Air compressor Before you dive into using an air compressor, you need to gather all the necessary materials. First and foremost, you’ll need the compressor itself. There are various types of air compressors available in the market, so you’ll need to decide which one is right for your specific needs.
Some compressors are suitable for small DIY projects, while others are designed for larger-scale industrial use. Once you’ve decided which type of compressor to purchase, make sure it comes with all the necessary equipment and accessories such as air hoses, air chucks, and fittings. These accessories are essential for connecting the compressor to your tools or other equipment.
Make a checklist of all the additional items you’ll need, such as safety goggles, gloves, and hearing protection, to ensure a successful and safe job. Picking the right materials may take some time, but it’s essential for a successful and efficient project.
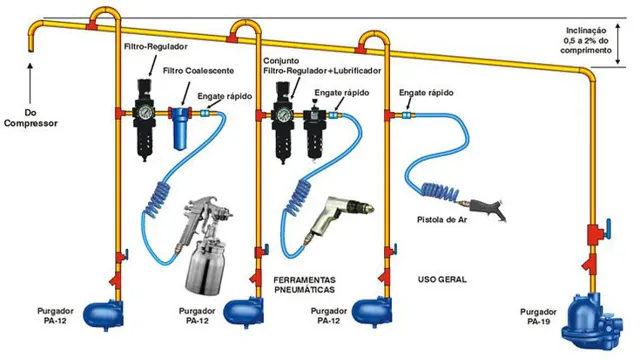
Fittings and couplers
When it comes to fittings and couplers, it’s important to gather the right materials. The type of fitting or coupler you need will depend on the specific application and the materials you are working with. Some common materials used in fittings and couplers include brass, stainless steel, and plastic.
It’s important to choose materials that are compatible with each other to avoid any corrosion or other issues. You’ll also need to consider the size and shape of the fitting or coupler, as well as any additional features such as quick-connect or push-to-connect capabilities. Taking the time to gather the right materials will help ensure a smooth and successful installation process for your fittings and couplers.
Hose
Hose Before starting any hose project, it’s essential to gather all the necessary materials. First and foremost, you’ll need a water hose, which varies in size, so be sure to choose one that suits your needs. You will also need a set of hose connectors, as this will enable you to link multiple hoses together or attach a hose nozzle at one end.
Hose nozzles are another necessity, and you can choose from a variety of options depending on your requirements. Whether it’s a watering wand for your garden or a pressure washer nozzle for cleaning your car, selecting the right nozzle will make your job much easier. Additionally, rubber washers are critical for preventing leaks where the hose connects to the nozzle or spigot.
Finally, always keep a hose reel handy as you don’t want to leave your hose tangled on the ground where it can be tripped over. With all the proper materials in hand, you can confidently start any hose project.
Teflon tape
When it comes to plumbing, using Teflon tape is an essential tool to ensure leaks don’t pop up and cause damage. But, before you start using Teflon tape, it’s crucial to gather your materials. Besides the tape, you will need a clean rag, a pipe wrench, and some thread sealant compatible with your plumbing materials.
Having these items is vital because you don’t want to be missing anything mid-project and have to run out to the store mid-task. It’s also recommended that you turn off the water supply before starting any plumbing project, just in case, as a way to prevent accidents and minimize the risk of water damage. By gathering the right materials beforehand, you can actively prevent issues.
Plan Your Line Setup
When it comes to setting up an air compressor line, planning is key. Before you start putting anything together, take a few minutes to think through how you want your line setup to work. Consider things like where you will be using your air tools, how many tools you will be using at once, and the distance between your compressor and your workspace.
With these factors in mind, you can determine the best placement for your compressor, choose the right type and size of tubing, and decide on the necessary fittings and connectors. By planning ahead, you can ensure that your air compressor line setup is efficient, effective, and safe to use. Oh, and don’t forget the importance of using high-quality components and following the manufacturer’s instructions carefully!
Determine the location of your compressor
Planning your line setup is an essential step when it comes to setting up an air compressor. One important aspect to consider is the location of your compressor. You want to ensure that your compressor is placed in a location that is free of any potential hazards, such as flammable materials or pollutants that could damage your compressor.
Additionally, you want to make sure that your compressor is placed in an area that is easily accessible and allows for efficient airflow. If the environment is too hot or too cold, it can affect the efficiency and performance of your compressor. Moreover, you want to make sure that your compressor is located in an area that has a stable power source and is not too far from the area where you will be using your tools.
By taking your time to carefully plan the location of your compressor, you can ensure that it operates safely and efficiently, and that your compressed air system performs optimally.
Measure the distance to your air tools
When setting up your air tools, it’s essential to measure the distance between them to plan your line setup. The distance between each tool will affect the overall efficiency of your pneumatic system. It’s important to remember that the farther away a tool is from the compressor, the more pressure drop there will be.
To prevent this decrease in pressure resulting from long air lines, you can use larger diameter hoses, which will help maintain a higher pressure level. Another alternative is to add secondary air regulators or air volume tanks close to the tools. This setup will allow you to have a steady flow of air at the tool’s point of use, optimizing its performance without overworking your compressor.
So, make sure to measure the distance, and choose the proper line configuration, hose size, and regulator to install your air tools correctly.
Determine the layout of your lines
When it comes to planning your line setup, it’s important to take into account the layout. This means considering the physical space that your lines will occupy and how they will interact with one another. You want to make sure that the lines are arranged in a logical and efficient manner, so that there’s no confusion or overlap when it comes to production.
Additionally, you need to think about burstiness, which refers to the variability in demand for your product. If you’re dealing with a highly volatile market, you need to be able to adjust your line setup on the fly to accommodate sudden spikes in orders. By considering both layout and burstiness, you can create a line setup that not only meets your production needs, but also allows for flexibility and adaptability.
Install the Fittings and Couplers
If you’re setting up an air compressor system, you’ll need to understand how to install air compressor lines. One of the most important steps in this process is installing the fittings and couplers properly. First, ensure that all threads are clean and free from debris.
Using Teflon tape or another thread sealant, wrap the threads a few times before attaching the fitting or coupling. Then, firmly tighten it in place with a wrench or pliers. Be careful not to over-tighten as this can damage the threads.
It’s also important to ensure that you’re using the correct type of fitting or coupling for your specific hoses or pipes to avoid leaks or other issues. Taking time to properly install these components will help ensure a safe and efficient air compressor system.
Attach quick-connect couplers to the compressor
When it comes to installing fittings and couplers for your compressor, attaching quick-connect couplers is an essential step. These couplers allow you to quickly and easily connect and disconnect air tools, hoses, and accessories from your compressor. To install them, start by ensuring that your compressor is turned off and disconnected from its power source.
Then, locate the air outlet port on your compressor and attach the female quick-connect coupler to it using a wrench. Next, attach the male quick-connect coupler to the end of your air hose by pushing it firmly onto the hose and securing it with a hose clamp. Finally, connect the male and female couplers by pushing them together until they click into place.
With your quick-connect couplers in place, you’ll be able to switch between air tools and accessories with ease, making your compressor even more versatile and efficient.
Install fittings on the hose ends
To properly use a hose, it’s important to have the right fittings installed at the ends. This involves selecting fittings that are compatible with the hose material and size, and then attaching them securely with the right tools and techniques. Some common fittings include couplers, connectors, adapters, and nozzles.
Couplers are especially useful for quickly connecting and disconnecting hoses, while adapters allow the hose to be connected to different types of equipment. When installing fittings, it’s important to follow the manufacturer’s instructions carefully to ensure a secure and leak-free connection. With the right fittings in place, a hose can be used for a wide range of applications, from watering a garden to delivering high-pressure fluids in industrial settings.
So if you want to get the most out of your hose, it’s important to pay attention to the fittings and couplers you use.
Wrap Teflon tape around all threads
When it comes to installing fittings and couplers, one critical step you should never forget is to wrap Teflon tape around all threads. This crucial step can make the difference between a successful installation and a leaking disaster. Teflon tape is a thin, white tape made from polytetrafluoroethylene (PTFE) that can help create a tight seal between threaded connections.
The tape acts as a lubricant that allows the threads to screw in more smoothly, while also filling any gaps between the threads that might otherwise lead to leaks. So whether you’re installing a new faucet, showerhead, or any other plumbing fixture, remember to wrap Teflon tape around each fitting and coupler before screwing them in. This will ensure a secure and leak-free seal, preventing any potential damage to your property.
So, always keep Teflon tape in your plumbing toolkit and make it a regular part of your installation process to avoid any costly damages in the future.
Attach the Hose to the Fittings
When it comes to installing air compressor lines, one essential step is attaching the hose to the fittings. To do this correctly, you’ll need to ensure that all the connections are secure and tight. First, identify the appropriate fitting for the hose end and check that it matches the diameter of the hose.
After that, you’ll want to lubricate the end of the fitting and insert it into the hose, applying pressure until it’s snug. You can use a hose clamp to secure the hose further and prevent any leaks. Repeat the process for the other end of the hose, attaching it to the compressor unit’s fitting, following the same guidelines to ensure it’s secure.
Remember, having a secure connection is crucial to ensure you get the necessary airflow to power your tools.
Push hose onto the fittings
In order to properly attach your hose to its fittings, it’s important to understand the process involved. To start, ensure that the fittings are clean and free of any debris or damage that could cause issues down the line. Once you have a clean surface, take your hose and push it onto the fittings, making sure to press firmly and evenly to create a tight seal.
Be sure to use a twisting motion as you push the hose into place to ensure that it is properly aligned and seated correctly. This may take a bit of effort, especially if you’re dealing with thick, heavy-duty hoses, but it’s important to get it right in order to prevent leaks and other issues. And with regular maintenance and proper care, your hose and fittings should last for years to come.
Slide hose clamps over the hose
When it comes to attaching hoses to fittings, slide hose clamps over the hose before securing it to the fitting. The hose clamp will help to ensure a tight and secure fit, keeping the hose in place and preventing leaks. To attach the hose, slide the hose over the fitting first, making sure that it fits snugly.
Then, position the hose clamp around the hose and tighten it until it is snug. Be careful not to over-tighten the clamp, as this could cause damage to the hose. Remember to use the appropriate size hose clamp for your particular hose and fitting to ensure a proper fit.
With this simple step, you can attach your hose to fittings with ease and prevent any potential leaks or mishaps. Keyword: hose clamp
Tighten clamps securely
When attaching a hose to fittings, it’s crucial to ensure that the clamps are tightened securely to prevent any potential leaks. The last thing anyone wants is for water or other liquids to burst out unexpectedly due to poorly attached fittings. But how do we ensure that clamps are tightened to the correct tension? Firstly, we need to select the appropriate size of clamp that corresponds to the diameter of the hose and fittings.
Then, we should position the clamp so that it sits evenly on the sections being joined. Finally, using a torque wrench or pliers, we can tighten the clamp until it is snug and can’t be rotated by hand. Remembering to tighten the clamps securely will guarantee the hose stays securely attached to the fittings, ensuring no accidents or mishaps occur.
Test the Compressor Lines
When it comes to installing air compressor lines, it’s essential to test them thoroughly to ensure they are working correctly. One way to do this is to use a pressure gauge to check the pressure levels in the lines. You’ll want to check the pressure at the compressor, at the regulator, and at the end of each line to ensure they’re all within the desired range.
Additionally, give the lines a thorough visual inspection to check for any leaks, kinks, or damage. Testing your compressor lines before you use them will help prevent any accidents or malfunctions, ensuring that your equipment runs smoothly and safely. So, take the time to test your air compressor lines, and you’ll be able to enjoy all the benefits that come with a well-functioning compressed air system.
Open the compressor’s air valve
If you want to ensure that your compressor is functioning properly, it’s important to test the compressor lines. To do this, start by opening the compressor’s air valve to release any pressure that may have built up inside the unit. Once you’ve done this, visually inspect the compressor lines for any signs of wear or damage.
Check for leaks and make sure that the hoses are securely fastened to the compressor. If you notice any issues, don’t hesitate to address them immediately. Taking the time to test your compressor lines can help you identify potential problems before they turn into major issues down the line.
So if you want to keep your compressor running smoothly, be sure to make this a regular part of your maintenance routine!
Check for leaks
When it comes to checking for leaks in your compressor lines, it’s essential to take a thorough approach. First, you’ll want to inspect each line carefully, looking for any signs of damage or wear. It’s also crucial to check all the fittings and connections to ensure everything is tight and secure.
Once you’ve visually inspected the lines, it’s time to perform a pressure test to check for any leaks. You can use a specialized tool to do this, which will help identify any areas that may need attention. By taking the time to properly test your compressor lines, you’ll be able to catch any potential issues early on, preventing costly repairs down the line.
Remember, regularly checking for and addressing leaks is key to ensuring the safe and efficient operation of your compressor.
Test air tools to ensure proper function
If you’re using air tools for any project, it’s essential to test the compressor lines to ensure proper function. You don’t want to waste your time and effort on non-working air tools and risk damaging your project. It’s always better to test everything first before starting.
Start by turning on the compressor and let the air pressure build. Then, turn off the compressor and check the pressure gauge. If the pressure drops significantly in a few minutes, you might have a leak in the compressor lines or fittings.
Try tightening the fittings to see if that resolves the issue, or investigate further to determine the cause of the leak. Testing the compressor lines before starting your project can save you time and money in the long run. Don’t skip this essential step, and make sure your air tools are in working order before you begin.
Conclusion
In conclusion, installing air compressor lines is a job that requires careful planning, attention to detail and a bit of elbow grease. But fear not, for with the right tools, knowledge and a little bit of humor, you can easily conquer this task and achieve the sweet symphony of compressed air flowing through your system. So, roll up your sleeves, grab your wrenches, and get ready to take on this challenge like a true pneumatic hero.
Remember, the secret to success is to keep things tight, stay lubricated and never forget to exhale. Happy compressing, my friends!”
FAQs
What tools are needed to install air compressor lines?
To install air compressor lines, you’ll need a compressor, hoses, couplers, fittings, Teflon tape, a wrench, and a pipe cutter or saw.
How do I choose the right size air compressor lines for my system?
The size of your air compressor lines will depend on the size of your compressor, the length of the run, and the tools or equipment you’ll be using. It’s best to consult a sizing chart or consult with a professional to ensure you choose the right size.
Can I install air compressor lines myself or do I need to hire a professional?
Installing air compressor lines can be done yourself if you have the tools and knowledge, but it’s recommended to have a professional install them if you’re unfamiliar with the process or if the system is large or complex.
How do I properly clean and maintain air compressor lines?
To clean and maintain air compressor lines, regularly drain moisture from the system, replace filters as needed, and inspect the lines for leaks or damage. Use a pipe brush and soapy water to clean the inside of the lines if necessary.
Can air compressor lines be installed outdoors?
Yes, air compressor lines can be installed outdoors, but be sure to use weather-resistant materials and take precautions to prevent freezing or damage from extreme temperatures.
What is the proper way to connect air compressor lines to the rest of the system?
Connect air compressor lines to the rest of the system using fittings or couplers, ensuring a secure and tight fit. Use Teflon tape on threaded connections to prevent air leaks.
Is it necessary to use a regulator in conjunction with air compressor lines?
A regulator is recommended to control the pressure of the compressed air and protect the system from over-pressurization. It should be installed downstream from the compressor and before any sensitive equipment.