Which of the following is true of welding machine settings? Tips for Optimal Performance.
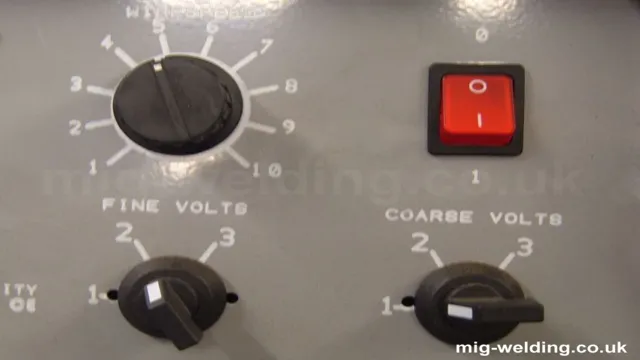
Welding is a highly skilled profession that requires precision, technical know-how, and the right welding machine settings. But understanding welding machine settings can be a daunting task for beginners. That’s why in this blog, we’ll break down everything you need to know about welding machine settings, including amperage, voltage, wire feed speed, and gas flow rate.
We’ll also provide tips on how to set your welding machine for different types of welding projects. So, if you’re new to welding or want to improve your welding skills, keep reading to learn the crucial welding machine settings that can help you produce high-quality welds.
Importance of Proper Welding Machine Settings
When it comes to welding, understanding the importance of proper welding machine settings is crucial. It can be tempting to simply set the machine to its default settings and start welding, but this can lead to poor weld quality and even safety hazards. Welding machine settings determine factors such as voltage, amperage, and wire feed speed, and finding the right combination for the specific metal being welded is critical.
Too high of a voltage or amperage can cause burn-through or distortion, while too low of a wire feed speed can lead to inconsistent welds or even cold lap. On the other hand, finding the proper settings improves weld quality and strength, reduces the likelihood of defects or errors, and overall lead to a safer work environment. So the next time you’re setting up a welding machine, take the time to adjust the settings for optimal results, and always prioritize safety.
Achieving Optimal Weld Quality
Proper welding machine settings can make a significant difference in achieving optimal weld quality. It’s crucial to set the right parameters to ensure that the weld is strong and durable, and the metals are properly fused. Welding parameters, such as voltage, current, and wire feed speed, dramatically affect the welding process and the final outcome.
Setting the correct welding parameters requires a good understanding of the equipment and the type of material being welded. It may take trial and error, but adjusting these settings will increase efficiency, reduce downtime, and produce consistent and long-lasting welds. Just like baking a cake, the ingredients need to be measured precisely, and the temperature needs to be set accurately to obtain the desired outcome.
The same goes with welding – the right settings result in a beautiful and robust weld. So, don’t underestimate the importance of proper welding machine settings.
Ensuring Welding Safety
Welding safety is of utmost importance, and one critical factor that contributes to it is setting the welding machine correctly. Having inadequate settings on the welding machine can lead to a lack of penetration, poor weld quality, and even accidents. When you set your welding machine, you need to ensure that the parameters align with the type, thickness, and position of the metal you’re working with.
This includes considerations about voltage, amperage, wire feed speed, and welding techniques to achieve a stable and proper welding arc. Properly set-up welding machines not only improve safety but also ensure that the finished product is of high quality, and meets the desired standards. So, it’s essential to understand the welding machine operation and manufacturer’s guidelines, and experience in welding to ensure that you are using the right settings and techniques for each job.
Factors to Consider When Setting Up Your Welding Machine
When it comes to setting up your welding machine, there are a few important factors to consider. Firstly, the type and thickness of the materials you will be welding will determine the voltage and amperage settings that you need to use. It’s essential to match these settings to the demands of the job, as choosing the wrong ones can result in weak welds, material damage, or even injury to yourself or others.
Additionally, the type of electrode or filler material that you use will also impact your welding machine settings. Generally, thicker electrodes require more amperage, while thinner ones need less. Another important factor to consider is your welding technique, as different techniques may require specific settings.
Finally, you should always read the manufacturer’s guidelines for your welding machine to ensure that you’re using it safely and effectively. Remember, setting up your welding machine correctly is crucial for achieving quality results, so take your time to do it right.
Type of Material Being Welded
When it comes to welding, one of the most important factors to consider is the type of material being welded. Different metals and alloys require different welding techniques and settings, so it’s crucial to choose the right setup for the job. Factors like the material’s thickness, conductivity, and melting point can all impact the welding process and determine what settings your welding machine needs to be on.
For instance, when welding aluminum, a higher amperage setting may be necessary due to the metal’s high conductivity. On the other hand, welding thicker materials like steel may require lower amperage but longer welding times to ensure proper penetration. By taking the type of material into consideration, you can set up your welding machine to ensure that you’re using the right settings for the job at hand, leading to better results in your welding project.
Electrode Size and Type
When setting up your welding machine, one of the most important factors to consider is electrode size and type. The electrode you choose will greatly impact the strength and quality of your welds. There are several factors to consider when selecting the electrode size and type, including the material being welded, the type of welding machine being used, and the thickness of the material.
For instance, if you’re welding a thinner material, a smaller electrode may be more appropriate, but if you’re working with thicker steel, a larger electrode may provide more effective results. Additionally, different types of electrodes have unique properties that can enhance the welding process. For example, a basic coated electrode is a good all-purpose choice and can weld a variety of materials.
On the other hand, a cellulosic coated electrode is ideal for vertical welding and offers a fast-freezing slag that creates a strong and stable weld. Thus, it’s important to understand the properties and benefits of different types of electrodes so you can choose the right one for your specific welding needs. Overall, selecting the right electrode size and type is crucial in ensuring that you achieve the best welding results possible.
By considering the material you’ll be welding and understanding the properties and benefits of different electrodes, you can set up your welding machine for optimal performance and produce high-quality welds with ease.
Power Source and Amperage
One of the most important factors to consider when setting up your welding machine is the power source and amperage. The power source is what provides the electricity needed to operate the machine, and it’s important to make sure that you have access to a reliable and adequate power source before you begin. You’ll also need to know the amperage requirements of your welding machine to ensure that it’s compatible with your power source.
Generally, the higher the amperage of your machine, the more power it will require. It’s important to note that using an insufficient power source can result in poor weld quality, reduced efficiency, and even damage to your welding machine. So, always double-check the power source and amperage requirements before you start welding.
Travel Speed and Angle
When it comes to welding, there are many factors to consider when setting up your machine. One of the most important factors to consider is the travel speed and angle. The travel speed is the speed at which the welding gun moves along the joint while the angle refers to the angle of the gun held by the welder.
The travel speed and angle must be carefully controlled to ensure a quality weld. If the weld moves too slowly, it can cause overheating and distortion, leading to a weak weld. On the other hand, if the weld moves too quickly, the weld may not penetrate enough and may result in a weaker weld.
In terms of angle, the angle of the gun can affect the shape and strength of the weld. Holding the gun at a higher angle can result in a narrower weld, while holding it at a lower angle can result in a wider weld. The angle can also affect the appearance of the weld, as a steeper angle can result in a more pronounced bead.
In conclusion, when setting up your welding machine, it is important to consider the travel speed and angle. With careful control of these factors, you can ensure a quality weld that is strong, even, and aesthetically pleasing. Remember to take your time and experiment with different settings to find the optimal travel speed and angle for your particular welding project.
Common Mistakes to Avoid When Setting Up Your Welding Machine
One common mistake to avoid when setting up your welding machine is assuming that all metals require the same welding settings. In reality, different metals require different amounts of heat and power to weld properly. It’s important to know the properties of the metal being welded and adjust the settings accordingly.
Another mistake is not properly cleaning the metal before welding. Any oil, grease, or rust on the metal can interfere with the welding process and result in a weak weld. Additionally, not properly grounding the welding machine can lead to electrical shocks or damage the equipment.
Finally, always be aware of the welding machine’s duty cycle and don’t exceed it. Excessive use can cause the machine to overheat and result in costly repairs. It’s important to take the time to properly set up and maintain your welding machine to ensure safe and effective welding.
Remember, understanding which of the following is true of welding machine settings is key to success in welding: different metals require different settings, proper cleaning and grounding is essential, and don’t exceed the machine’s duty cycle.
Wrong Electrode Type or Size
When setting up your welding machine, it’s crucial to use the right electrode type and size to ensure the best welding results. One common mistake that many novice welders make is using the wrong electrode type or size for the job. This can lead to weak welds, poor penetration, and even damage to the welding equipment.
Choosing the correct electrode type and size depends on the type of metal being welded, the required weld strength, and the type of welding machine being used. Using the wrong electrode can lead to a multitude of problems, such as the electrode being too weak for the metal being welded, or the electrode heating up too quickly, causing the weld to become molten and ineffective. On the other hand, using an electrode that is too large can cause difficulty in controlling the welding arc and lead to a lack of precision in the weld.
That’s why it’s crucial to understand the basics of electrode selection and use. It’s important to invest time in researching and learning about different electrode types and sizes to make an informed decision. This will not only save you time and frustration, but it will also result in strong and reliable welds.
In summary, don’t make the mistake of using the wrong electrode or size when setting up your welding machine. Do your research, take the time to understand electrode selection, and choose the right one for the job. By doing so, you can avoid poor welds and damage to your equipment, resulting in a job well done.
Incorrect Amperage Setting
One of the most common mistakes welders make is an incorrect amperage setting. This is a crucial aspect of welding that can affect the quality of your weld. When the amperage is too high, it can cause the weld to be too hot, leading to warping and distortion.
On the other hand, when the amperage is too low, it can create a weak and incomplete weld. To avoid this mistake, it’s important to understand the material you are welding and the thickness of the metal. You should also consult the manufacturer’s recommendations for your welding machine.
Remember to adjust the amperage as needed for each project to ensure a strong and durable weld. By avoiding this common mistake, you can improve your welding skills and produce high-quality results.
Conclusion: The Importance of Proper Welding Machine Settings
In conclusion, determining the correct welding machine settings is key to achieving a successful weld! It’s important to understand that no two welding projects are the same, so careful consideration must be given to factors such as the type of material being welded, the thickness of the material, and the joint configuration. Additionally, the skill level of the welder, environmental conditions, and even the welding machine itself can all play a role in the appropriate settings to utilize. As with most things in life, trial and error is essential for finding the right balance.
So, if at first, you don’t succeed with your welding machine settings, try, try again!
FAQs
1. What are the basic settings for a welding machine? A: The basic settings for a welding machine include selecting the appropriate current type and level, wire feed speed, and voltage. 2. How do I determine the correct welding machine settings for a specific job? A: Factors to consider when determining welding machine settings for a specific job include the type and thickness of the material being welded, the type of joint being used, and the welding technique being employed. 3. Can I use the same welding machine settings for different types of welding? A: No, different types of welding require different machine settings. For example, MIG welding requires a different voltage and wire feed speed than TIG welding. 4. What is the purpose of the heat input setting on a welding machine? A: The heat input setting allows you to control the amount of heat being applied to the weld, which can affect the weld penetration and the overall quality of the weld. 5. How do I adjust the arc length on a welding machine? A: To adjust the arc length on a welding machine, you can increase or decrease the voltage or the electrode stickout length until you achieve the desired arc length. 6. What is a duty cycle and how does it affect welding machine settings? A: The duty cycle refers to the amount of time a welding machine can operate continuously before needing to cool down. Machines with a high duty cycle can generally be used at higher settings for longer periods of time without overheating. 7. What safety precautions should I take when adjusting welding machine settings? A: Always wear appropriate personal protective equipment such as welding gloves, eye protection, and a welding helmet. Additionally, be sure to follow the manufacturer’s instructions for adjusting machine settings to avoid injury or damage to the machine.